Animaking is a pioneering Brazilian animation studio known for its innovative use of traditional and digital techniques in stop motion animation. In 2013 they released Worms (Portuguese: Minhocas) a stop motion animated adventure fantasy comedy film. It is the first Brazilian stop-motion animated film.
This post explores the innovative techniques and processes I had the pleasure to work on during my time as Production Supervisor at Animaking. The text and images are derived from a scientific article I wrote and presented in 2018 at the 13th Congress of Research and Development in Design (13 Congresso de Pesquisa e Desenvolvimento em Design) in Joinville, Santa Catarina, Brazil.
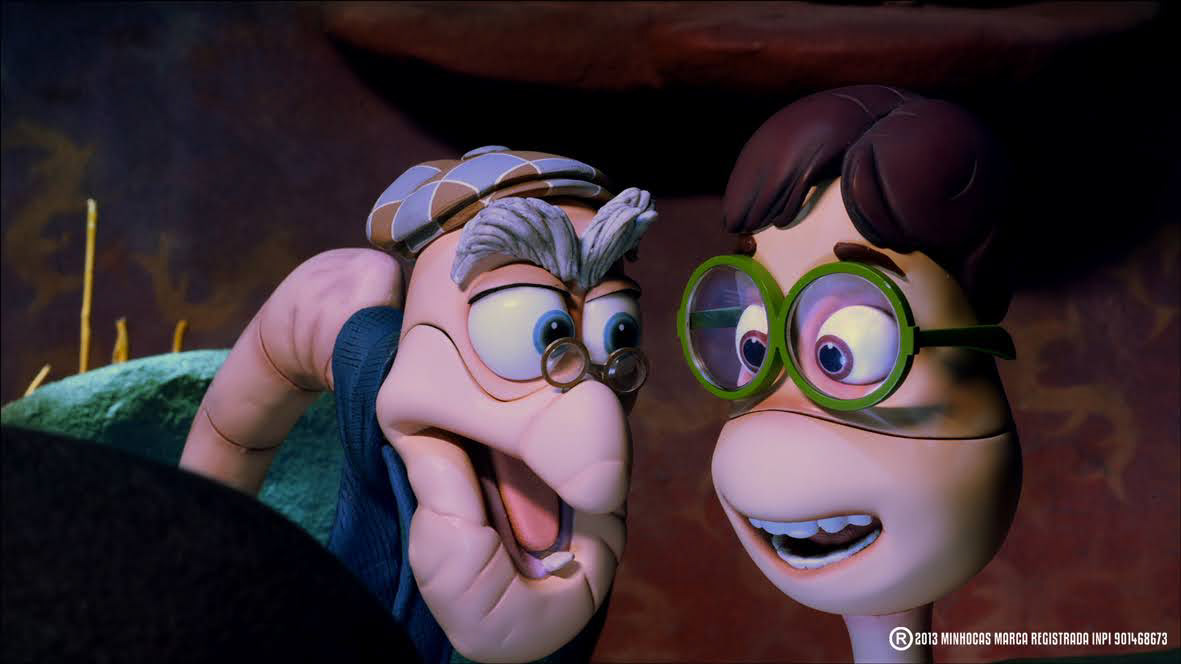
Initially, Animaking's approach involved manually sculpting all character models and then scanning them. After scanning, we performed retopology in a 3D software to create various mouth variations. Each frame of the animation required a unique 3D printed mouthpiece to achieve precise lip-syncing and expressive character animations.
In the image below you can see the clay sculpture, the scanning process and the 3D model.
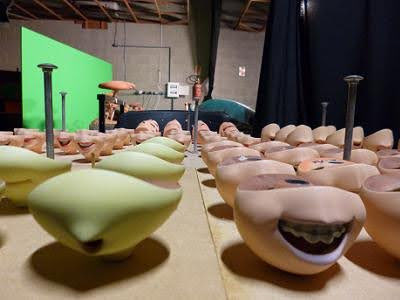
Example of the amount of mouths created for the film Worms (2013)
In 2017/2018, we embarked on a new venture: a short movie to test a novel solution for the characters' mouths. We decided to introduce digital sculpture into our workflow. The flexibility and control offered by digital tools resulted in more detailed characters. Fine details were challenging to achieve with clay sculpture due to the small size and manual handling, as the average character head in the Worms project is 8 centimeters tall.
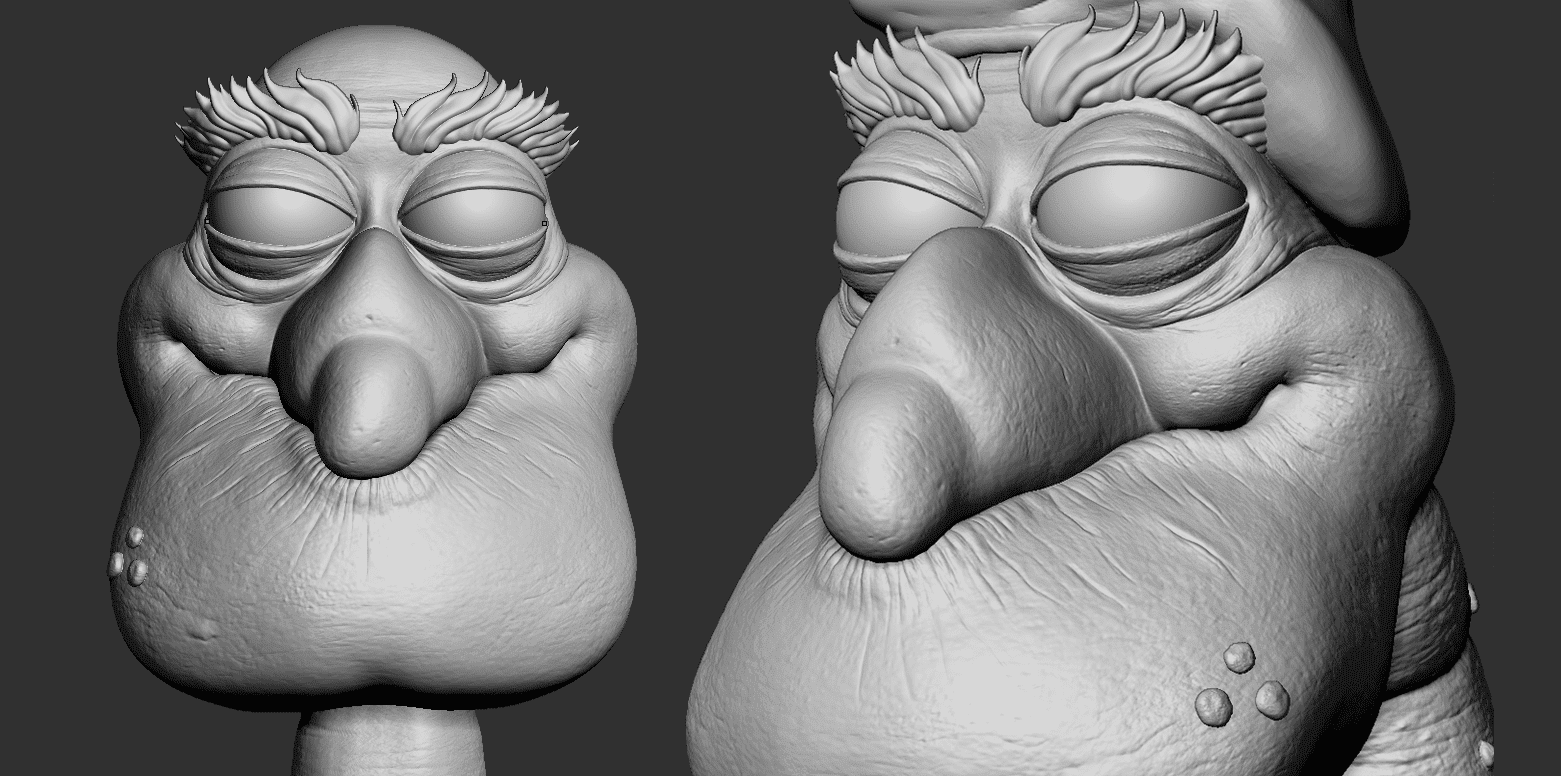
The challenge with the replacement technique is the large volume of pieces required. To reduce the number of mouth replacements, we designed an articulated rod that could function like a jaw, giving each mouth a range of motion previously achieved only by sequentially using multiple printed mouths. This rod articulates the mouth up to a point where a different shaped mouth is needed, resulting in a more dynamic and flexible animation with fewer mouth replacements.
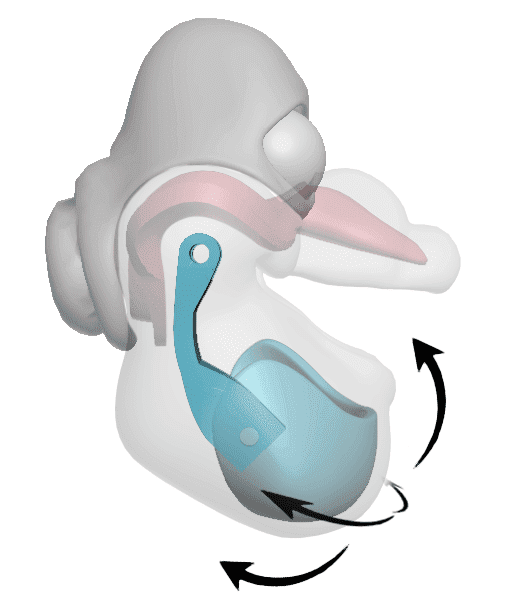
Mouth joint design.
This articulation is only possible with mouths made from flexible materials like silicone using molds. Instead of directly printing the mouth in its positive form, the technical innovation suggested was to design the entire mold structure digitally. By using computational resources to subtract the modeled mouth volume from a solid piece and printing the pre-sculpted negative mold, we streamlined the process.
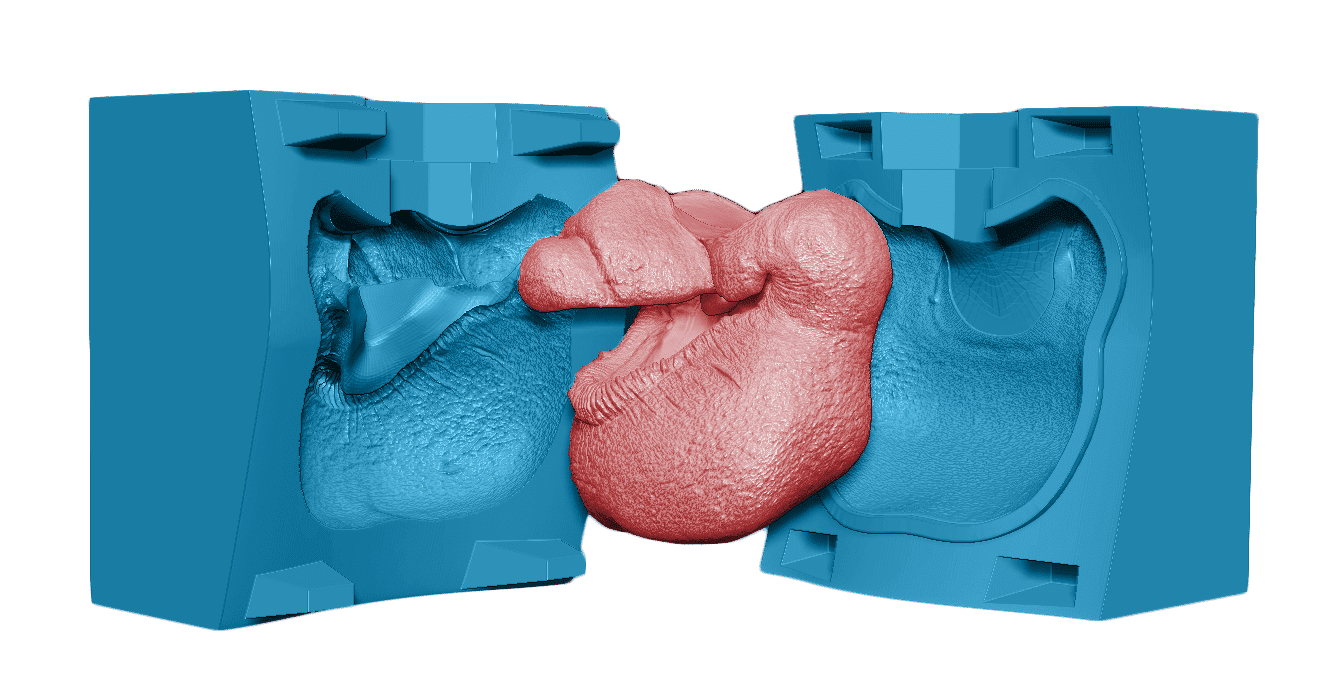
In blue the parts that will be printed and in red the mouth used to subtract the structure in blue.
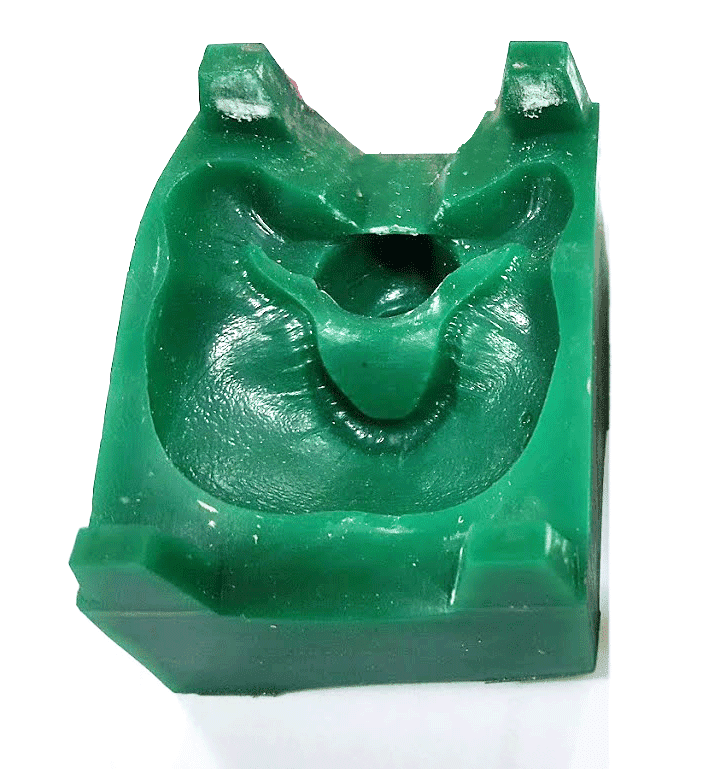
Mold printed in photosensitive resin on the Wanhao D7 printer
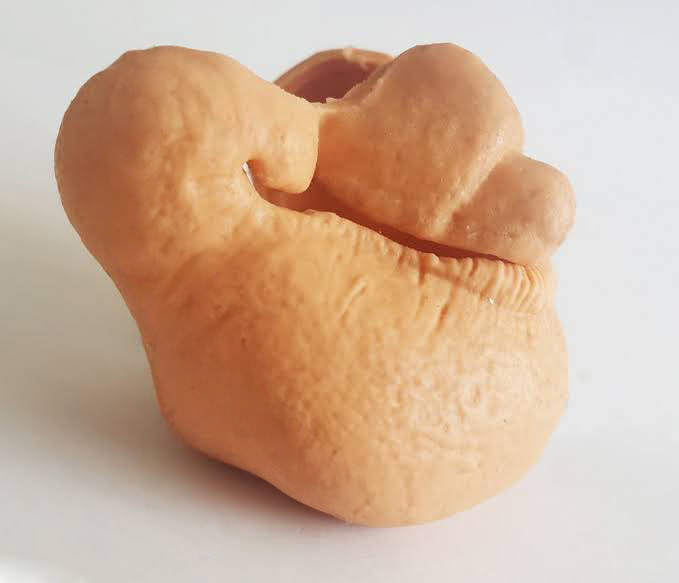
Silicone mouth crafted using a mold
In Animaking's animation tests, the use of articulated exchangeable mouths gave animators greater freedom and allowed for more dynamic and fluid movements with a limited number of mouthpieces. For example, the following image shows nine frames where the animator achieved nine different mouth positions using the same exchangeable mouth. In traditional replacement animation, these nine positions would require nine different mouthpieces, regardless of the minimal variations
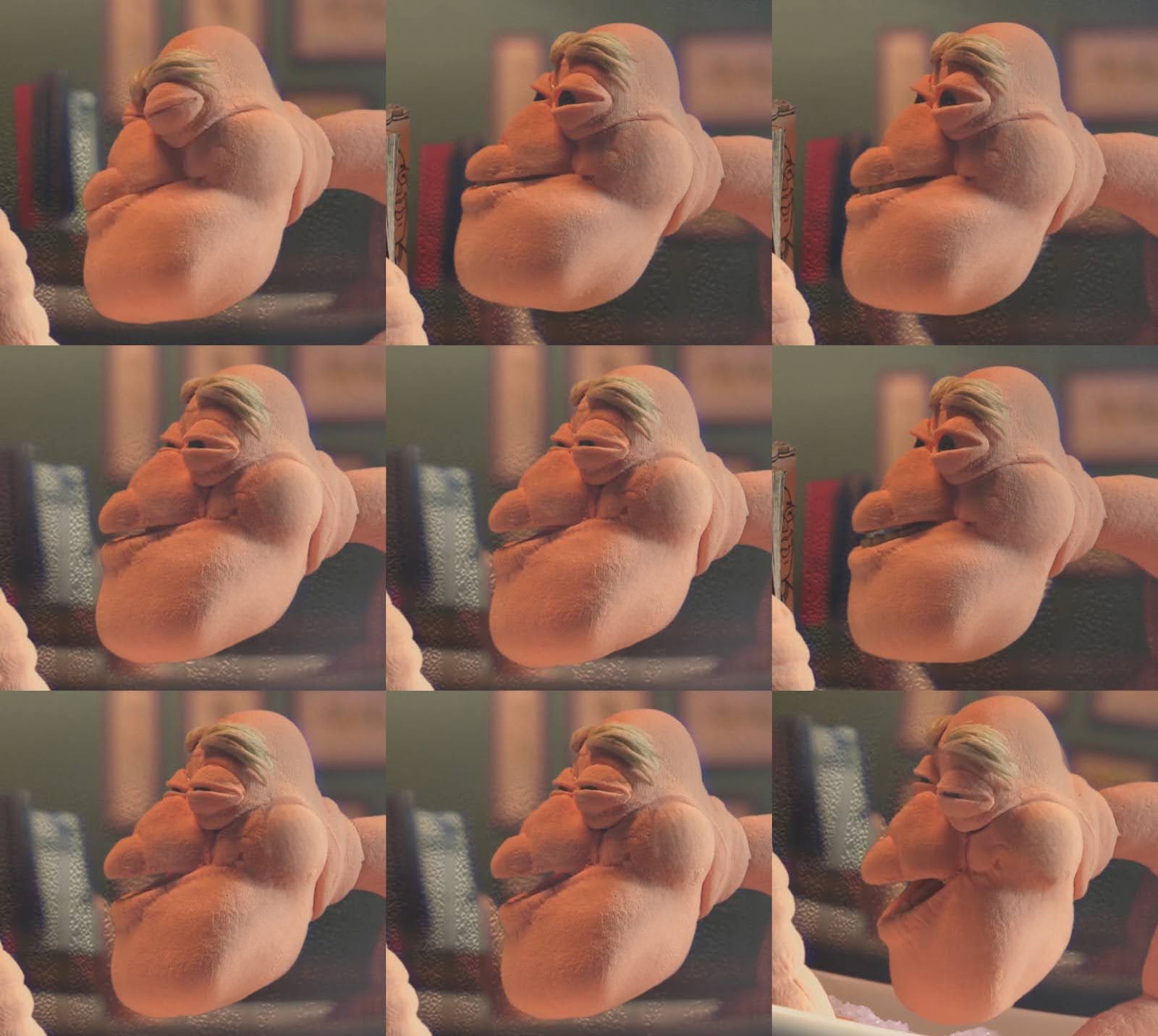
As an indirect result of using articulated exchangeable mouths, the silicone provided characters with a more realistic and sophisticated visual outcome. The interaction of silicone with light resembles the way light interacts with human skin, adding a positive aspect to the new film.
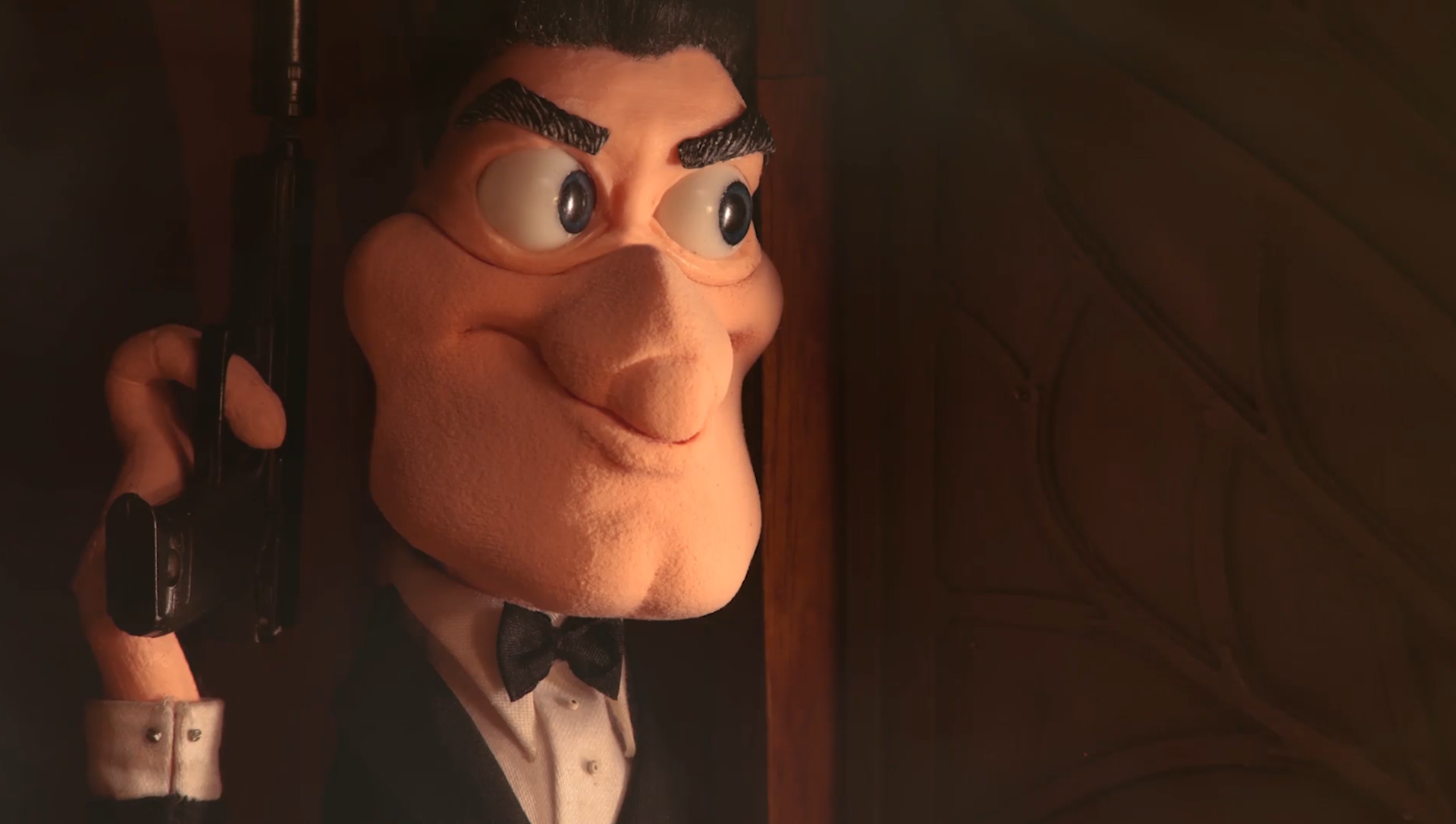
All the rights reserved to Animaking Studios LTDA